
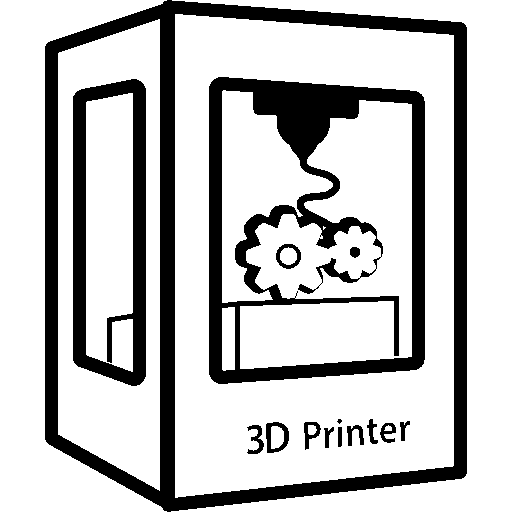
IMO having the ability to do TPU is way more versatile than going to another rigid structural filament.
ABS/ASA is just “pla but more impact resistant”.
TPU is “haha funny squishy wait this turns into a living hinge?” and opens up a TON of print opportunities.
I had a lot more fun trying out TPU (both high and low durometers) than switching to any other kind of filament. Whatever you print basically becomes shockproof l, is squishy/bendy, and you can chuck it across a room full-force with no problems. Super fun.
However, TPU is happiest with a direct drive extruder. High durometer (95a) TPU’s are fine, but not optimal, in bowden extruders, while low durometer (Ninjaflex) straight up won’t print right thru a bowden. So keep your type of printer in mind when shopping for spools of test filament.
PLA basically doesn’t dissolve in any (readily available consumer-grade) solvents. Your best bet is going to be to take the entire unit as far apart as you can until it is metal only components, heat it with a heatgun to make the PLA soft/melt, and brush it all off with a brass cleaning brush.